Color Difference Analysis of Injection Molding
Color difference usually occur during injection molding production.The reason for the color difference of injection molding is caused by the following aspects: raw materials, molds, process parameters, equipment, environment, personnel, etc. We can use the handheld colorimeter to control the injection color difference.
I. Color difference analysis of injection molding
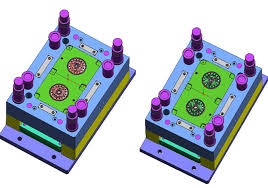
1. Color masterbatch affect injection molding color difference
For the color masterbatch, we have to conduct a random color test before mass production. It must be compared with the last proofreading and compared in this time. If the color difference is not large, it can be considered qualified. Just as the batch color masterbatch has a slight color difference, the masterbatch is remixed before use to reduce the color difference caused by uneven mixing of the masterbatch itself.
2. Injection molding machine and mold affect injection molding color difference
If the color difference is caused by the injection molding machine, it is generally caused by factors such as the pouring system and the exhaust groove. In order to avoid this effect, the injection molding machine should be regularly checked and maintained.
3. Production process affect injection molding color difference
For example, when the handheld colorimeter measures color, the change is very large, but it is not the caused by the color difference measured by handheld colorimeter. This requires adjustment of the injection molding process parameters, as far as possible without changing the injection temperature, back pressure, injection cycle and color masterbatch. At the same time, the adjustment also needs to observe the impact of the process parameter changes on the color and luster. If color difference is found, it should be adjusted in time.
4. Injection temperature and back pressure affect injection molding color difference
In the production, we often encounter large changes in the measurement results of the handheld colorimeter due to a certain heating ring damage or failure, or the heating control part is out of control and the burning causes the barrel temperature to change drastically. The color difference caused by this kind of reason is easy to determine, so it is necessary to check the heating part frequently in production and replace and repair it in time when the heating part is damaged or out of control to reduce the probability of such color difference.
II. What to do when the color is uneven during injection molding?
Poor mixing of plastic masterbatch with the same color masterbatch will also make the color of the product volatile. After the masterbatch and the masterbatch are mixed mechanically and then fed into the hopper through the lower suction. The masterbatch is separated from the masterbatch due to static electricity and is easily adsorbed on the hopper wall.
This situation can be solved by taking the raw materials into the hopper and then manually mixing them. For adding colored toner to produce colored products, the most effective method is not to use a suction machine, but to use a hot air dryer, using manual feeding method to prevent the color difference caused by the separation of the toner and the masterbatch.
In the specific coloring operation, the colorant composition and the proportion of additives will affect the appearance color of the final product. In order to make the color difference of the plastic material within a reasonable range, the common method in the industry is to use a handheld colorimeter to control the color difference of plastic materials.