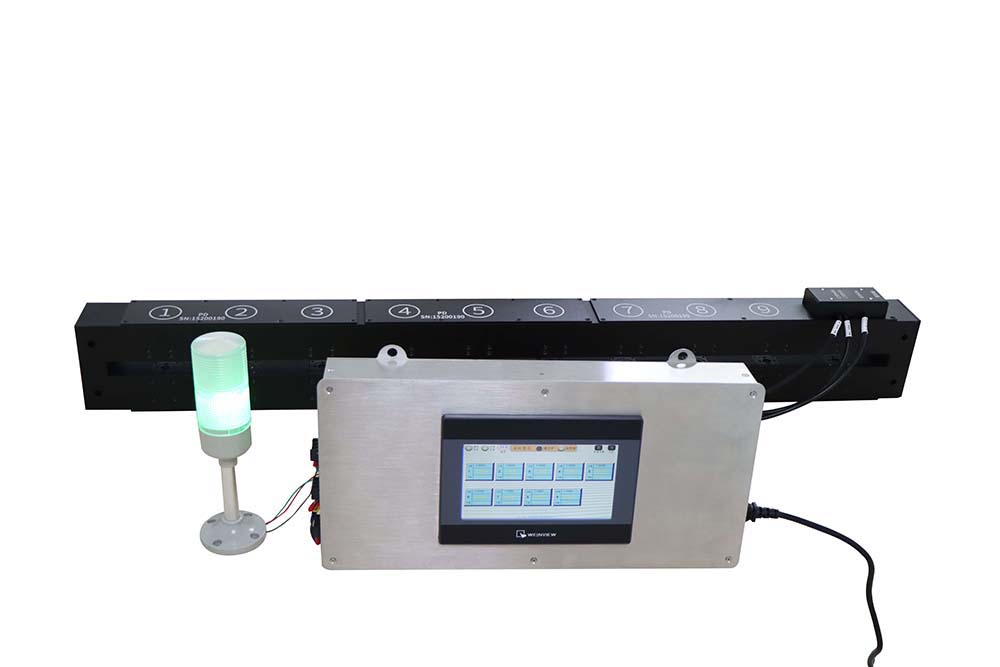
LS153 Vacuum Coating Thickness Measuring System
Online thickness measurement equipment for concentration coating machine, online monitoring of material uniformity
Independent digital probe design, easy to operate and install
Two-way RS485/MODBUS, can be connected to PLC, HMI and PC
High measurement accuracy and good stability of test data
Free to choose the size and number of test points, 45 test points can be customized at most
The vacuum coating thickness measuring system works in the principle that the transmittance (optical density) of the material at a specific wavelength of light is proportional to the coating thickness. The uniformity of the material is achieved by monitoring the optical transmittance (optical density) of the material. The thicker the coating, the higher the optical density and the lower the transmittance. As long as the light can pass through the material, the product quality can be controlled by monitoring the transmittance (optical density).
The device is able to measure the thickness of the coating layer of the product online in real time, which helps to grasp and monitor the quality of the product in the production process, find out the problems and adjust the process as early as possible, so as to improve the quality of the product and reduce the rate of scrap. This vacuum coating thickness measuring system is widely used in concentration vacuum coating machine, glass coating, glass production line, coating production line and other fields.
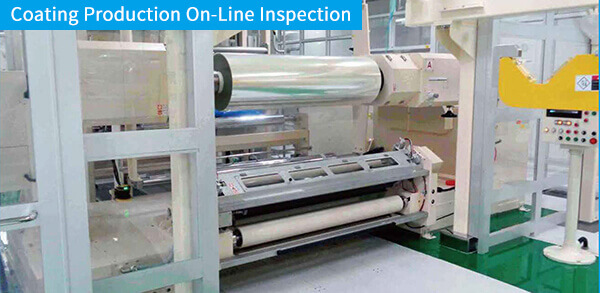
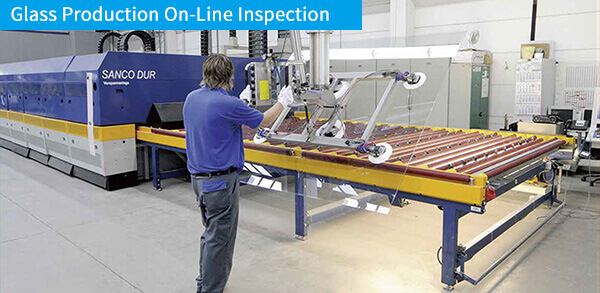
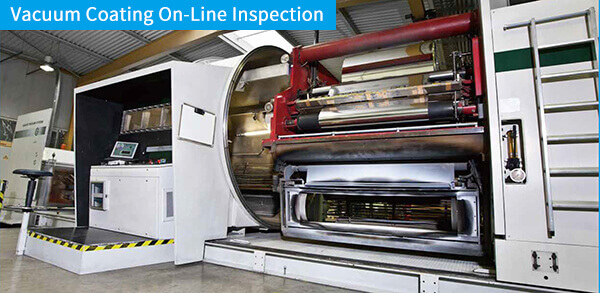
Note: LS153 vacuum coating thickness measuring system is an upgraded model of LS152. LS152 has one controller to control 3 sets of probes and the signals are processed by the controller. LS153 signals are processed in the probes without the need of a controller.
LS153 Vacuum Coating Thickness Measuring System Introduction
Size and number of monitoring points can be customised
The user can freely choose the number of test points, up to 45 test points can be customised. The actual length of the device is based on the number of customized test points.
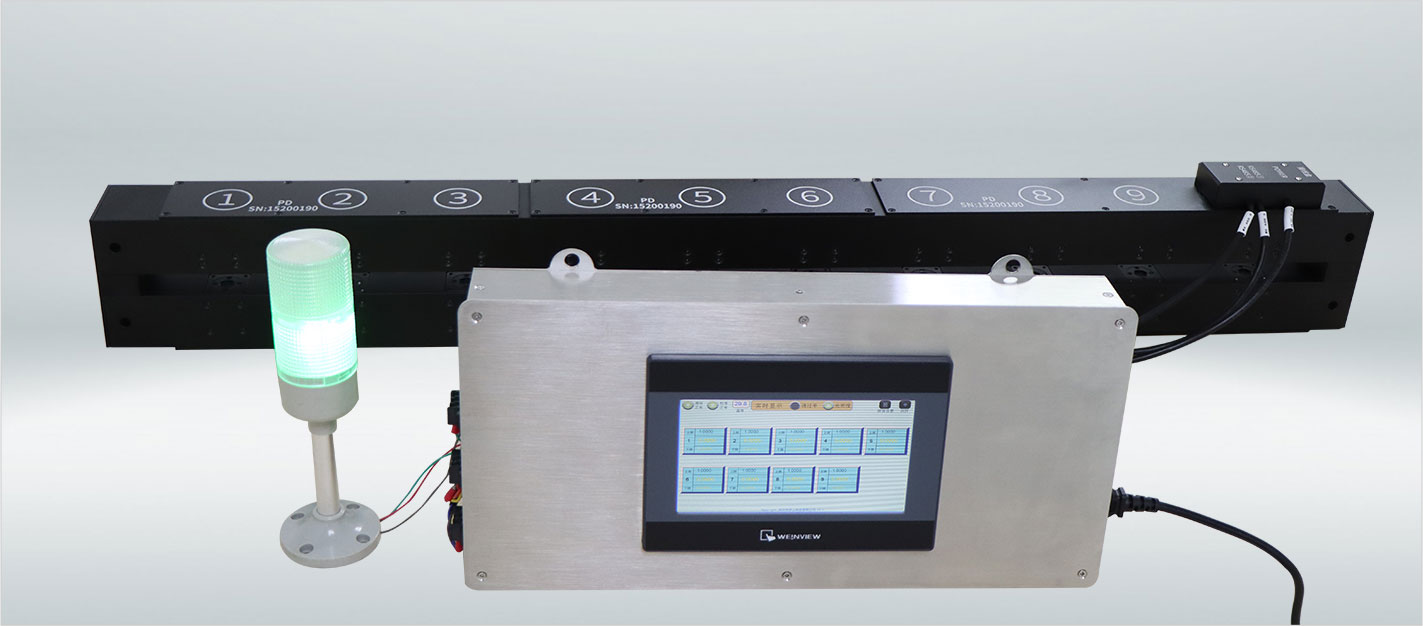
RS485 communication interface/MODBUS communication protocol
The instrument provides dual RS485 communication interface and standard MODBUS communication protocol, which is convenient for communication with PLC, Single Chip Microcomputer, human-machine interface, kingview, computer and so on. The optical density data can be read on the coating machine to realize control automation (closed-loop control).
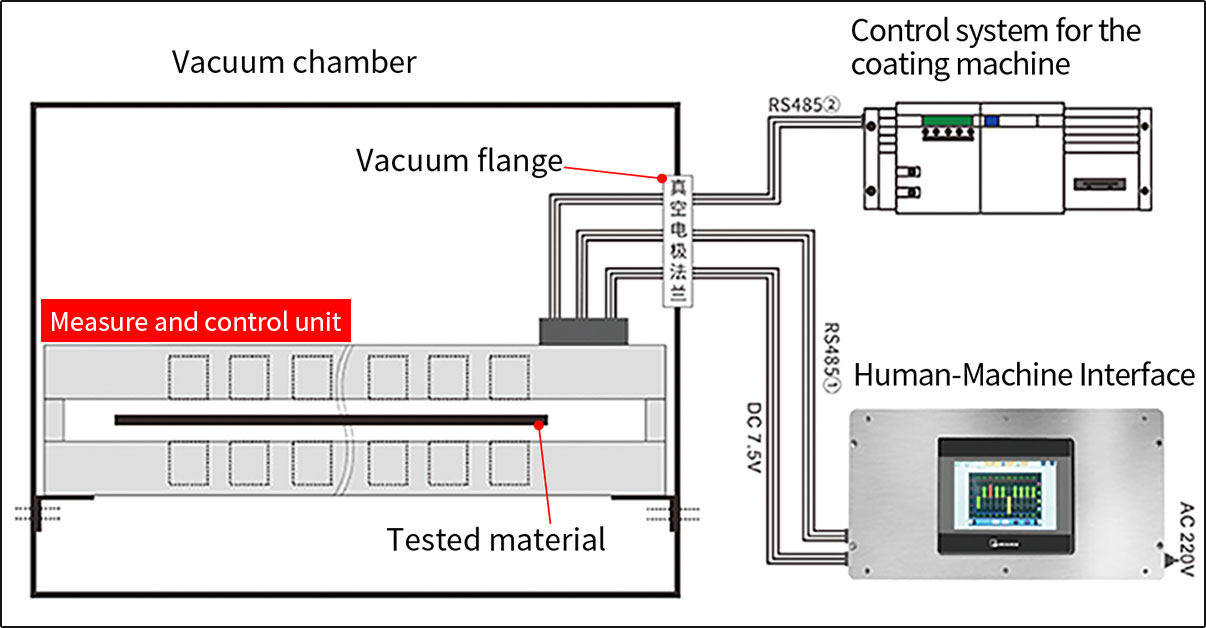
System Composition
The equipment is mainly divided into three parts: measure and control units, human-machine interface, computer real-time monitoring software (optional).
Measure and control units
They mainly includes light source probe, receiving probe, controller, aluminum profile frame.

Independent digital probe design, easy to operate and install
A set of probes contains a light source probe and a receiver probe, with 4 mounting screw holes on the light hole side and 4 mounting screw holes on the side of the probe for easy installation.
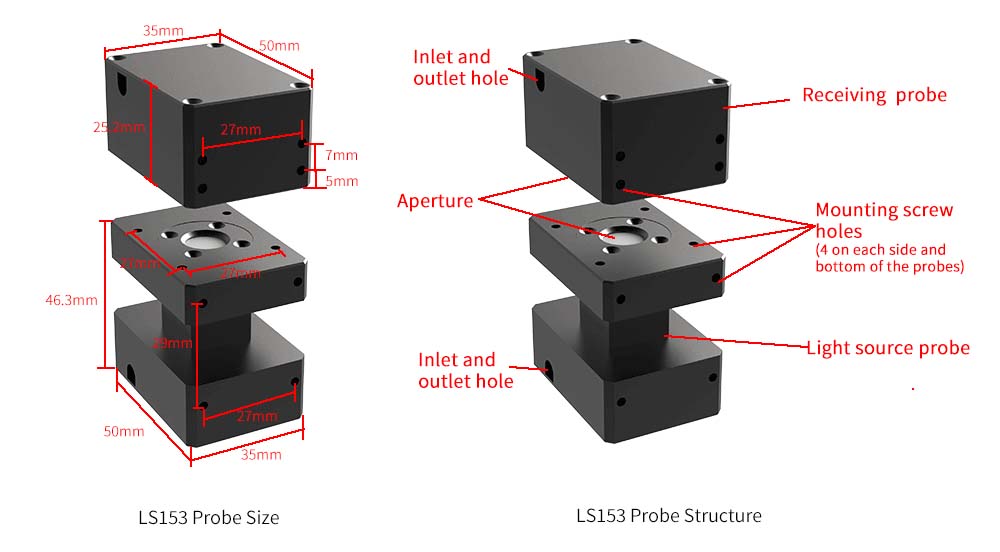
Human-machine interface
There are 3 types of HMI control boxes to choose from: recessed, wall-mounted and desktop (detailed drawings will be provided for confirmation at the time of ordering).
Computer real-time monitoring system (optional)
Real-time monitoring of the data, including real-time display, histogram, setting of upper and lower limits, real-time curve and alarm when the limit is exceeded. The transmittance and optical density display can be switched freely.
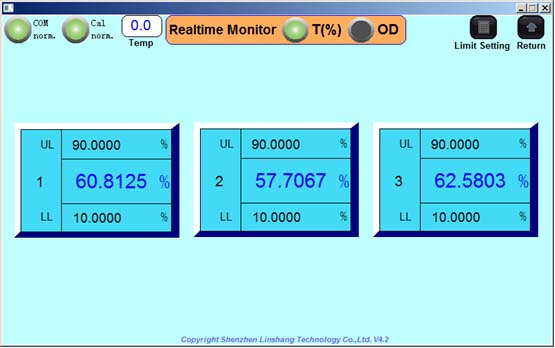

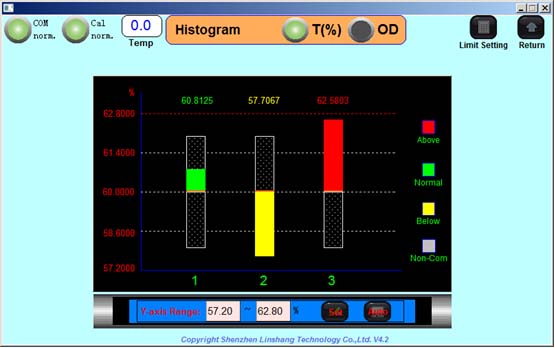
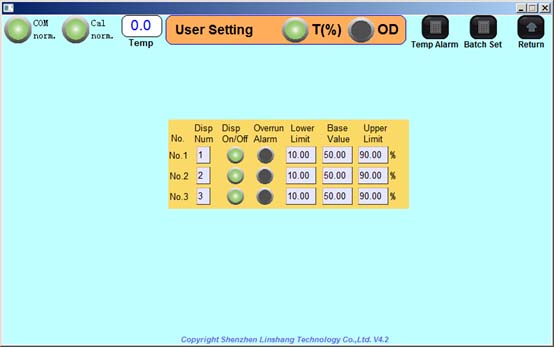
Control console and installation method
The controller and the test probe are embedded in the control console and only need to fix the control console during installation. Each device is equipped with a bracket, which is customized according to the actual installation needs of customers.
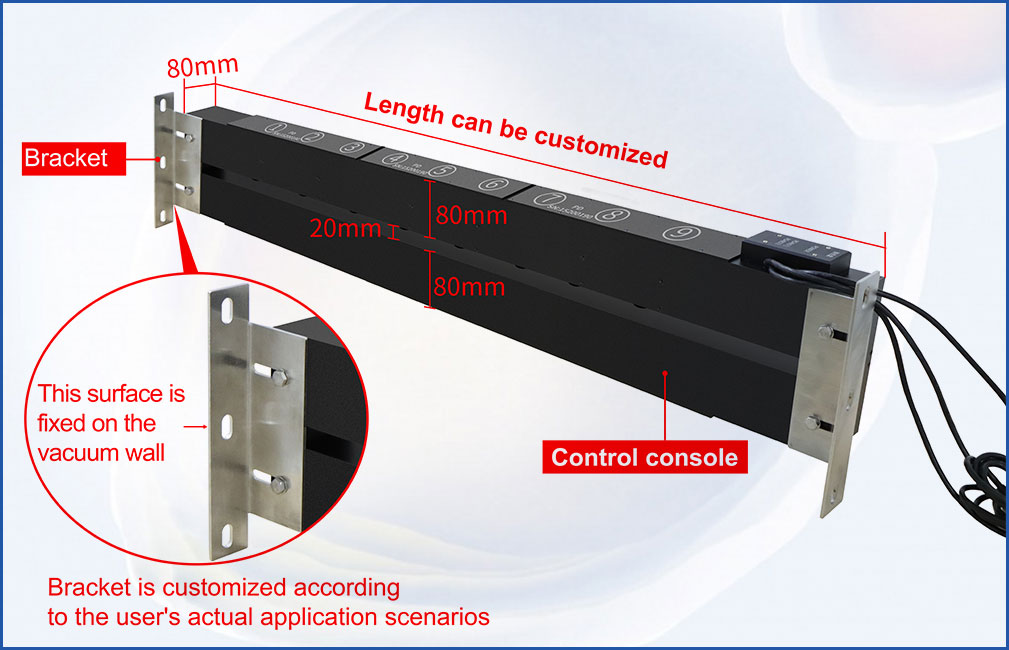
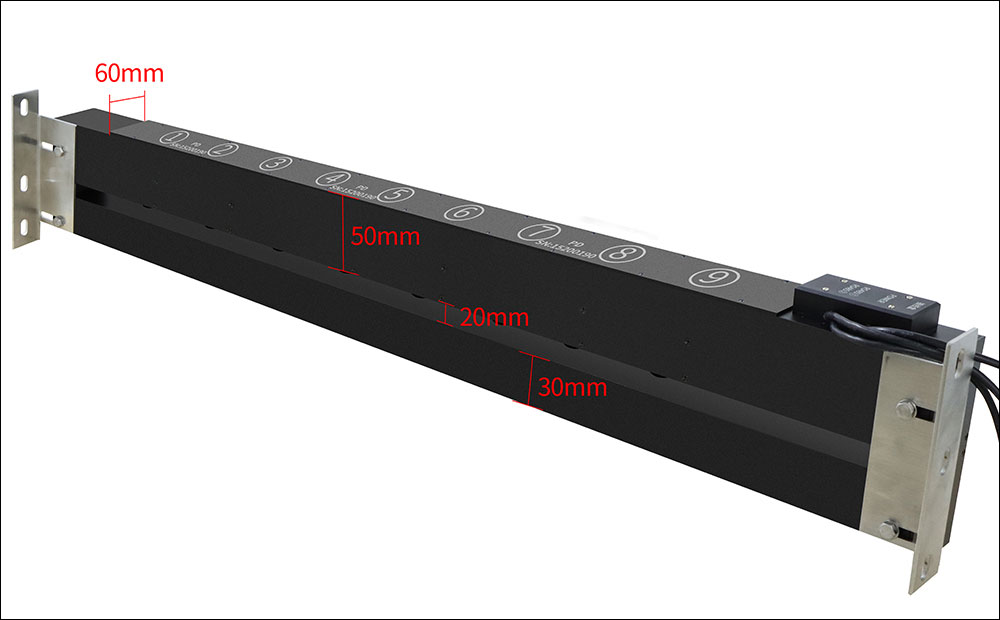
Features
1.Ultra-small digital probe, super easy to use and install, only 6 wires to be connected.
2.The instrument use optical non-contact measurement, without direct contact with the test material. It will not cause damage to the tested material.
3.RS485 interface and MODBUS communication protocol, which is convenient for communication with PLC, Single Chip Microcomputer, human-machine interface, kingview, computer and so on, and can achieve closed-loop control by communicating with the coating machine.
4.The vacuum coating thickness measuring system has high measurement accuracy.
5.The instrument use modular design, each module is connected by aviation connector, single point is removable, which is convenient for future maintenance.
6.With dust-proof design, dust does not affect the inside of the gyroscope. Customers just need to clean the front glass of the probe.
7.The instruemtn has over-limit alarm function and can intelligently control production quality. The instrument can reduce dependence on manual operation and improve production efficiency and quality.
8.The instrument has a temperature compensation function, the value is stable, allowing the use of high-temperature environments.
9. The instrument is equipped with automatic calibration and manual calibration function, which can be freely set by the user according to the need.
10.Equipped with human-machine interface, real-time monitoring of the data, including real-time display, histogram, upper and lower threshold settings, over-limit alarm, RS485 ② communication parameter settings, etc. The transmittance and optical density display can be switched freely.
System Parameters
Parameters | LS153 |
---|---|
Test Wavelength (Optional) | Green light: 530nm; Infrared: 850nm |
Measuring Spot | 5mm |
Transmittance Measurement Accuracy | ±1% |
Transmittance Resolution | 0.005% |
Optical Density Measurement Range | 0.00 OD - 6.00 OD |
Optical Density Resolution | 0.01 OD for 0.00-3.00 OD 0.05 OD for 3.00-5.00 OD 0.15 for 5.00 - 6.00 OD |
Maximum Measurement Points | 45 points |
Distance Between Adjacent Probe | Minimum distance of 35mm |
Distance Between Receiving Probe and Light Source Probe | 20mm |
Temperature Range | -10°C - 60°C |
Storage Temperature | -20°C - 70°C |
Relative Humidity | less than 85%, no condensation |
Data Refresh Cycle | Normal mode 300ms/ Fast mode 100ms |
Communication Interface | Dual RS485 |
Communication Protocol | MODBUS protocol |
Dimension | 80mm(W)*180mm(H)*L (Customized) |
Vacuum Flange Electrode Cores | 6 ( RS485①+DC7.5V) 9 ( RS485①+ RS485②+DC7.5V) |
Power Supply | 220V AC/50Hz |
Operation Video
Industry Solutions
Solution for checking the thickness of common aluminised films
Aluminised film is made by vacuum aluminising process in which very high purity aluminium wires are evaporated to gaseous state at high temperature(1100°C to 1200°C). Afterwards, when the plastic film passes through the vacuum evaporation chamber, gaseous aluminium molecules will be deposited on the surface of the plastic film, thus forming a glossy film with a high metallic color. The LS153 vacuum coating thickness measuring system is capable of inspecting large quantities, widths and lengths of aluminised films at one time.The test bracket is installed on the device to realise on-line automatic testing, real-time monitoring of data, alarms for exceeding the limits, and transmission to the coating machine via RS485 to provide equipment support for the closed-loop control of the coating machine.
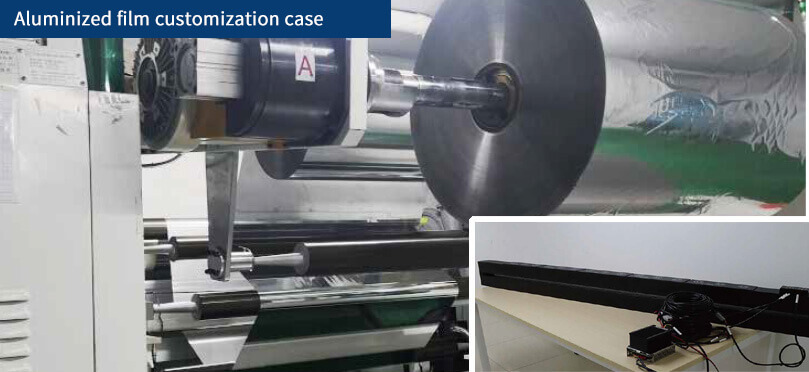
Solution for detecting the thickness of zinc sulphide films
Zinc sulphide films are mainly made by thermal evaporation. The vacuum coating thickness measuring system is using the principle that optical density and coating thickness are in a certain proportion. Through monitoring the optical transmittance (optical density) of the zinc sulphide film to achieve the purpose of monitoring the its uniformity, some manufacturers use 365nm or 530nm light source solutions
for zinc sulphide film thickness testing.
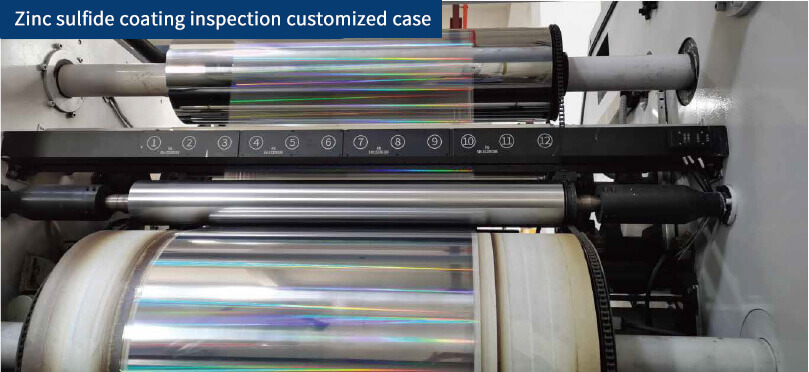
Solution for detecting the thickness of copper-plated films
Copper plating film is generally applied to flexible substrates (PET and other materials), through the use of magnetron sputtering coating machine to let the surface of the substrate deposition of a layer of high-purity oxygen-free copper conductive layer, so that the surface of the material has a conductive, thermally conductive properties. With the LS153, you can easily understand the coating condition and adjust the process parameters of the coater in real time, saving time and cost.
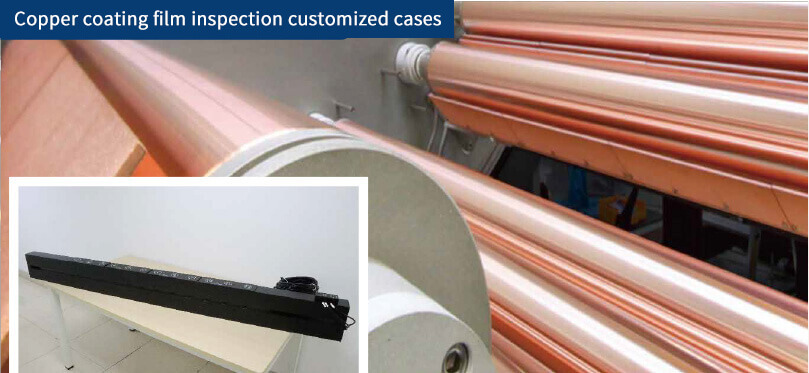
Solution for testing glass transmittance
On-line inspection of coated glass is a new technology. LS153 can detect the film thickness, uniformity and light transmittance of glass on the production line in real time, which can avoid producing glass products that do not meet national standards. Real-time detection and real-time processing can avoid unnecessary losses, save costs and increase productivity.
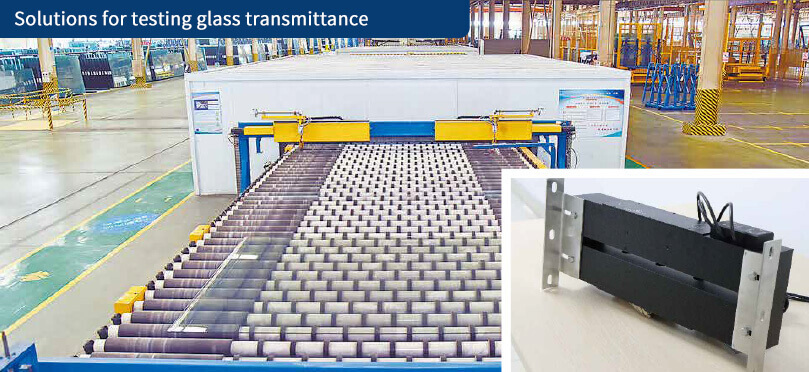
Solution for checking the thickness of gold-plated foils
Gold foil is a very valuable material, using LS153 to detect whether the thickness of gold foil is uniform in real time during the process of gold plating can greatly reduce the waste of materials and save costs. The instrument adopts the diffuse transmittance principle and uses the opal glass method to test not only flat transparent light-transmitting materials, but also the uniformity of coating thickness on frosted,
milky-white and other substrate films.
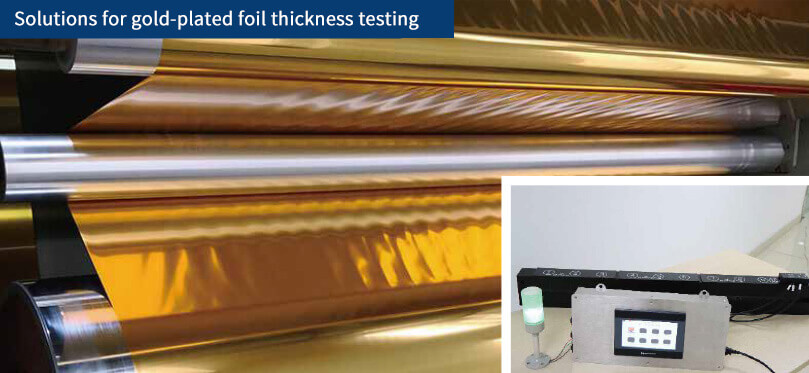
Your product information request
Please let us know your requirements and we will be in contact with you shortly!